2015-10-21
Taiwanese bottler opts for aseptic PET line from Sidel
Posted By: News Deskon: October 21, 2015
Taiwan Hon Chuan Enterprise has installed the country’s first Sidel Combi Predis FMa Capdis line, creating the capacity required to provide flexible aseptic production and meet the evolving tastes and demands of consumers for sensitive products.
The Sidel Combi Predis FMa Capdis, an aseptic blow-fill-cap solution with dry decontamination of both preforms and caps, is operating at Hon Chuan’s plant at Taichung on the island’s western coast. It is used for the bottling of a range of low-acid to high-acid products, such as RTD tea, milk tea and coffee in 350ml, 450ml and 600ml PET bottles in round and rectangular formats. It has an output rate of 40,000 bottles per hour.
While delivering the vital reliability in food safety and hygiene for co-packer Hon Chuan, it provides a solution that is highly competitive, offers faster production with lower costs and dramatically reduces use of energy, resources and chemicals, thereby contributing to the company’s ambitious sustainability goals. The Sidel Combi Predis FMa Capdis also had to be flexible enough to manage frequent changeovers as bottle formats, shapes and product recipes change several times a week.
It is quicker than Hon Chuan’s existing aseptic PET line equipped with traditional wet bottle decontamination, which runs at 36,000 bottles per hour. Sidel said that the team at Hon Chuan is pleased with the performance of the new line and, in particular, its contribution to increasing sustainability in production and reducing operating costs.
The system offers the Taiwanese company further advantages in a fiercely competitive marketplace, as it seeks to enhance its position as the island’s leading beverage packaging manufacturer – despite overall beverage sector contraction of 2% between 2013 and 2014.
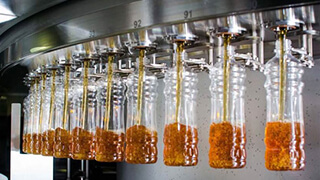
Hon Chuan chairman Keith Dai said: “As a co-packer, the challenge for us is to improve our production efficiencies to help our clients get their products on the market as and when they need to. Improving our capacity and maintaining flexibility to respond to the needs of the market are key to our success.With the recent acquisition of the aseptic Combi solution equipped with dry preform decontamination in Taiwan,we benefit from lower operating and maintenance costs to lighter bottles and reductions in energy.”
Based on a 6,000-hour operation with 85% overall efficiency, the bottler is set to save more than 40,000 litres of chemicals, 32,500 tonnes of water and 3,600 tonnes of steam. Aseptic line testing took place a few months after the installation was completed. These tests checked the microbiological validity with high acid and low acid products. The final commissioning was completed only five weeks after the line started up and the first commercial run took place shortly after.
Mr Dai continued: “We have been an early adopter of aseptic solutions in Taiwan.
To date, we have installed four aseptic lines with Sidel across Asia, producing more than 20 products for several leading beverage companies. We are more than satisfied with the results. “
We are constantly working towards reducing waste, energy and raw material cost.
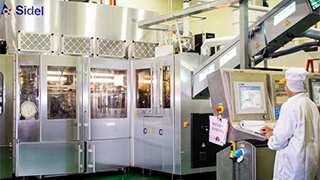
Technology plays a key role and we are glad we chose Sidel’s Combi Predis FMa Capdis for our latest aseptic line.
Predis dry preform decontamination ensures high hygiene for sensitive beverages while offering cost- effectiveness along with product and environmental benefits.